Clean room validation

Clean room validation
Clean rooms are critical environments in industries such as pharmaceuticals, biotechnology, electronics, and food processing, where the control of airborne particulates, microbial contamination, and environmental conditions is essential. we specialize in Clean Room Validation Testing, ensuring that your clean rooms meet stringent regulatory standards and provide optimal conditions for manufacturing, research, or product development.
What is Clean Room Validation?
Clean room validation is the process of testing and verifying that a clean room or controlled environment meets the specified cleanliness standards and operates within defined parameters. This includes assessing air quality, particle count, temperature, humidity, and microbiological contamination to ensure the environment is suitable for its intended purpose.
Our Clean Room Validation Services
We offer a comprehensive suite of testing services to validate clean rooms and controlled environments, including:
- 1. Particle Count Testing
- Objective: To measure airborne particles in various size ranges (e.g., 0.3 µm, 0.5 µm, and 5 µm).
- Purpose: Ensures the clean room meets ISO cleanliness classifications (ISO 1 to ISO 9) based on the number of particles per cubic meter of air.
- Method: Airborne particle counters and real-time monitoring systems.
- 2. Microbial Monitoring and Testing
- Objective: To detect microbial contamination (bacteria, fungi, and viruses) in the air, on surfaces, and within materials.
- Purpose:Verifies that the clean room maintains acceptable levels of microbial contamination, critical for sterile manufacturing environments.
- Method: Air sampling, surface swabs, and settle plates, followed by laboratory culturing.
- 3. Airflow and Air Velocity Testing
- Objective: To verify proper airflow, ventilation, and air exchange rates within the clean room.
- Purpose: Ensures that air flows in a unidirectional or turbulent manner, as required by clean room classifications.
- Method: Use of anemometers and airflow mapping tools.
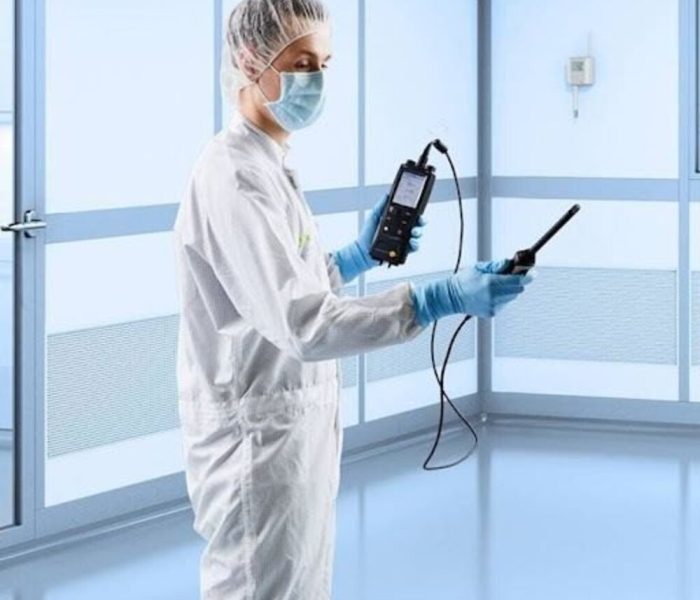
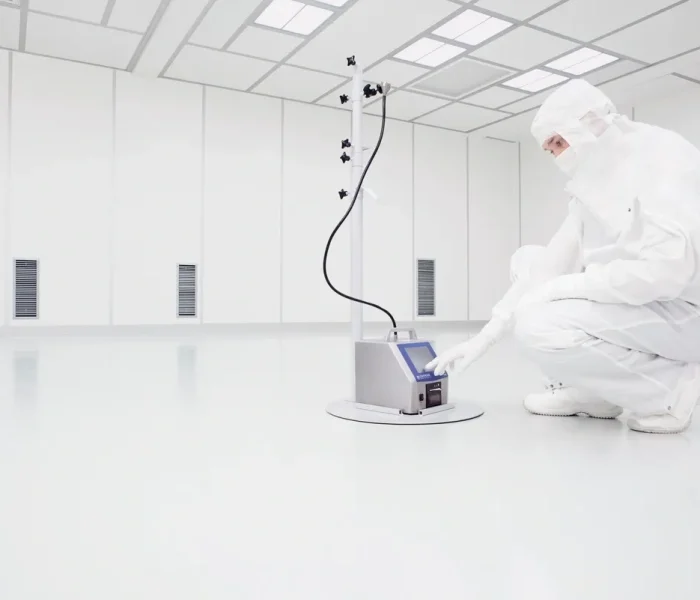
- 4. Temperature and Humidity Testing
- Objective: To monitor and control temperature and humidity levels within the clean room.
- Purpose: Ensures environmental conditions are maintained within the required range for product integrity and personnel comfort.
- Method: Continuous environmental monitoring using calibrated sensors.
- 5. Smoke Studies
- Objective: To visually inspect air circulation and verify airflow patterns.
- Purpose: Ensures there are no dead spots, turbulent areas, or short-circuiting of airflow that could compromise clean room integrity.
- Method:Non-toxic smoke generators used in combination with visual inspection.
- 6. Surface Cleanliness Testing
- Objective: To verify the cleanliness of surfaces and materials used within the clean room.
- Purpose: Ensures that surfaces do not contribute to particle or microbial contamination.
- Method: Surface swabs, wipe tests, and ATP (Adenosine Triphosphate) testing for cleanliness.
- Why Clean Room Validation is Important
- Regulatory Compliance: Clean room validation is essential for complying with industry regulations and standards such as ISO 14644, GMP (Good Manufacturing Practices), and FDA guidelines.
- Product Quality & Safety: Maintaining the correct environment is critical to ensuring product quality, preventing contamination, and avoiding costly recalls or production delays.
- Operational Efficiency: Regular validation ensures that clean rooms operate at peak efficiency, maintaining airflow, temperature, and cleanliness conditions that are crucial to the success of sensitive manufacturing processes.
- Risk Management: By validating clean room environments, you reduce the risk of contamination, cross-contamination, and failure to meet product specifications.
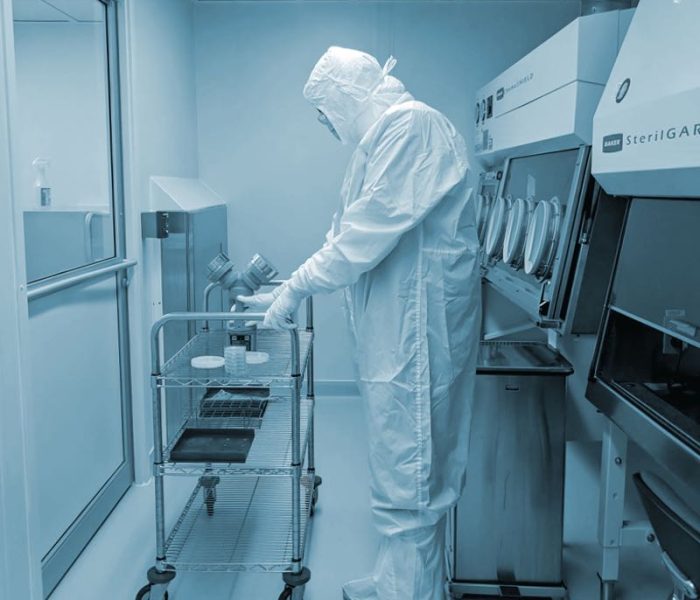